Alive HQ Recording Studio Redesign
Alive Network's in-house recording studio was recently redesigned from the ground up. We now have a fantastic air conditioned acoustically optimised control room, a new live room, Neve, API........
Over the last 5 months we've been redesigning our Alive HQ Recording Studio which is housed within the Alive office complex. The redesign has been a major investment for us but one which we hope will prove a success for both us and our bands.
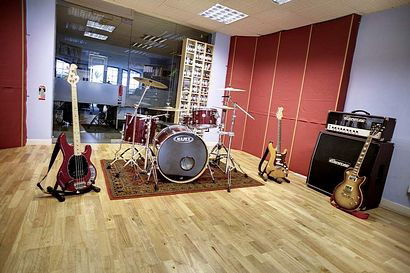
So what's new?
First off, we got expert studio design advice from Peter Keeling at Studio People. Pete visited our studio back in March and helped us put together a design plan which he felt would make best use of the space we have, and explained what was required to get the best possible acoustic treatment of each space. Pete's company could have managed and installed the whole redesign project, but our budget was tight and we were keen to buy a ton of new gear, so we opted to complete all the work ourselves, based on Pete's advice.
Stage 1 - to re-arrange the layout of the control room so the mixing desk was 1/3 along the length of the room, rather than positioned in the middle of the width of the room. This helped ensure the best distribution of sound reflections for our size/shape of room, and created a better space for our outboard racks behind the listening position. We also had an air conditioning unit fitted to keep things cool. It used to get very hot in here!
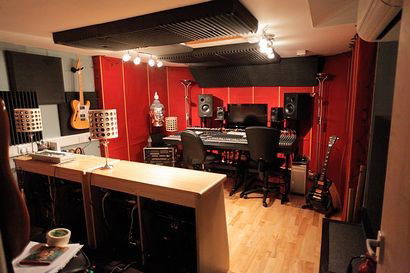
(Above - new control room layout)
(Below - the new air conditioning unit for the control room)
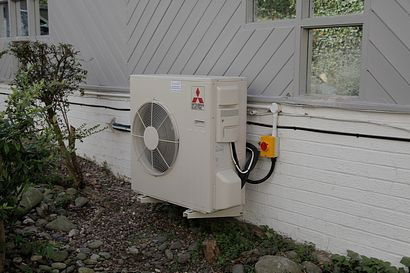
Step 2 - we installed a real hardwood wood floor into the control room, introducing some high end reflections back into the space to stop it sounding un-naturally dead. It also looks great!
Step 3 - we fitted custom designed acoustic treatment panels behind the mixing desk. For this we used 20cm thick Rockwool slabs, floor to ceiling, wrapped in a C shape around the entire mixing desk area and listening position. The slabs we held in place with a wooden frame which was then covered with a breathable red fabric. The specially treated walls ensure that a wide range of frequencies are absorbed at the listening position so that they don't reflect back at the engineer, colouring the sound.
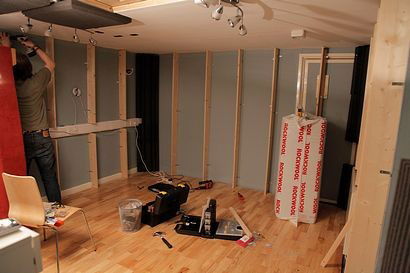
(Above - fitting the floor and acoustic treatment)
(Below - Rockwool slab acoustic treatment in place)
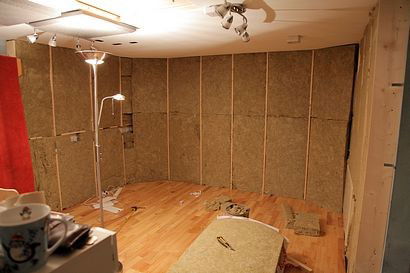
(Below - Red fabric covering the Rockwool acoustic treatment)
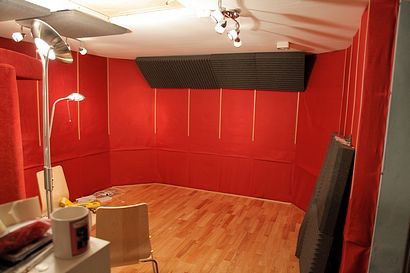
Step 4 - we created a dual use live room in one of our main office spaces. In the day, Alive Network staff use the room as a normal office space. In the evening/weekends, the desks move easily out of the way to provide an acoustically treated, spacious live room which can accommodate a 5 piece band with ease. The live room also has a real hardwood floor and custom built acoustic treatment.
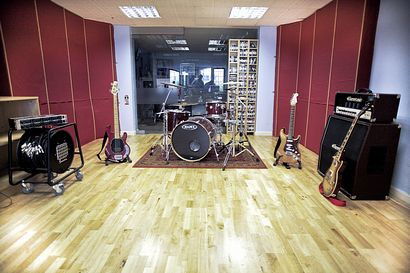
Step 5 - we redesigned our overdub booth with another... you guessed it...real hardwood floor and custom built acoustic treatment. The overdub booth is situated immediately to the rear of the control room, and also now has nice mood lighting and a Persian rug!
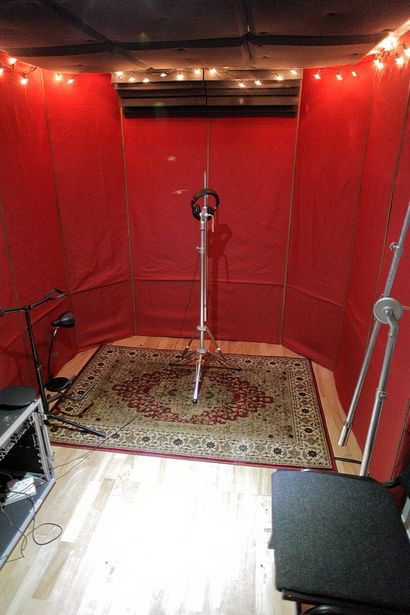
Step 6 - upgraded studio monitor speakers. After recording at Assault and Battery 2 in London, we decided that their Dynaudio BM15A nearfield monitors were amazing, so we bought a pair on eBay for a bargain price and they sound just as great as we remembered.
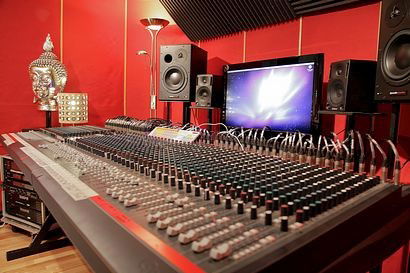
Step 7 - the big gear hunt! We very much enjoyed the process of shopping around for all the pieces of boutique outboard gear that we'd added to our wish list over the years. Some of the new equipment purchased for our outboard racks included Neve 1073 pre-amps, Neve 8803 stereo EQs, API 512 pre amps, API 550b EQs, Universal Audio 610 MKII pre-amp and compressor, Steven Slate Pro Audio Dragon Compressor, Empirical Labs EL8 Distressor.
We also got a bunch of new mics, including Neumann KM184 stereo matched pair, SE Rupert Neve 1 ribbon mic, AKG 414 B/TLII stereo pair amongst others.
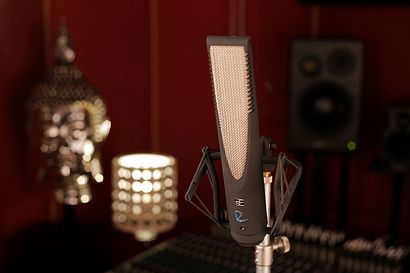
All of our new outboard gear was racked into two custom built realwood racks, made to order by the guys at StudioRacks.
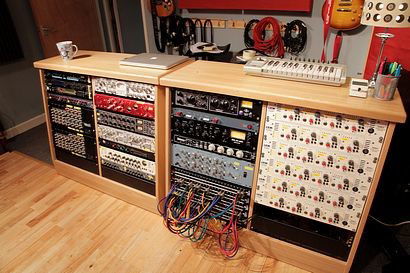
Step 8 - re-wire! The very costly process of re-wiring began once everything was in its new home. The patchbays and insert wiring alone cost over £4000, far more than we expected, though the effort was well worth it. Everything is now exactly where we want it, and we can patch any item of gear onto any channel on the desk in about 5 seconds.
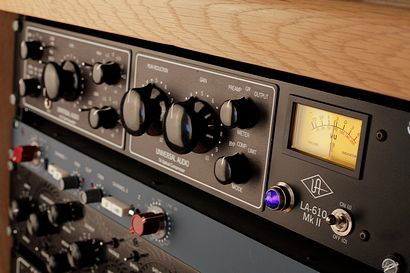
Step 9 - the final major upgrade was to move over to ProTools 9 running on a high spec Mac Pro. This should have been straightforward except for the fact that ProTools 9 doesn't seem to like our combination of audio interfaces, and so it took a few days of head scratching (and swearing) to find a workaround we were happy with.
We're happy to say we got there in the end!
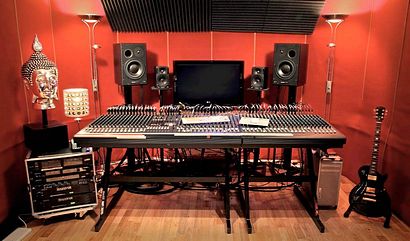
The studio has now been open for a few weeks and the results from the revamp have been incredible. The new pre-amps make a world of difference to the recorded sound quality, and the acoustic treatment and room optimisations have massively improved the usability of the space.
To book time at Alive HQ, give us a call on 01782 740839.
There's a 40% discount for Alive Network artists, which means a full day costs only £150 plus VAT!
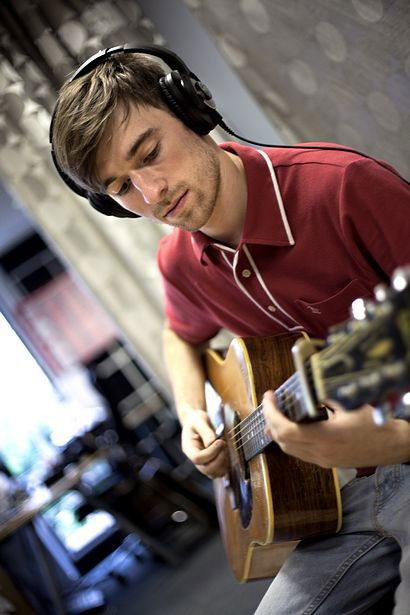
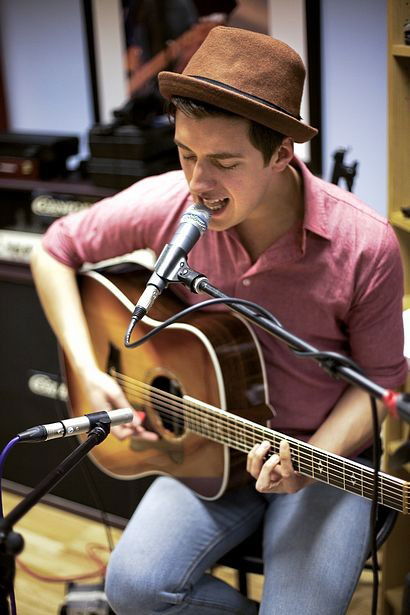
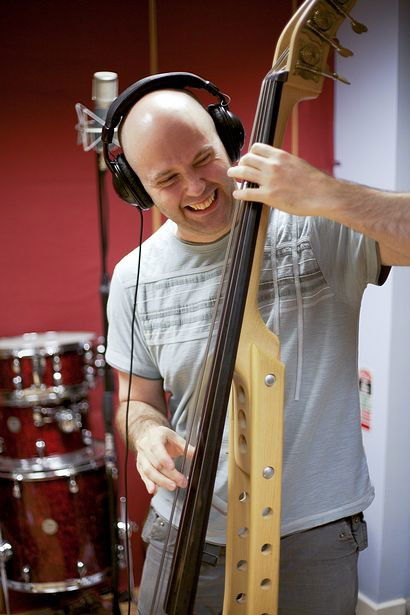